Common failure modes or issues associated with Roulements à rouleaux coniques à une rangée appariés include:
1. Défaillance par fatigue : causée par un chargement cyclique répété conduisant à la formation de fissures dans les composants du roulement.
2. Dommages à la surface : dus à une lubrification inadéquate, à une contamination ou à des particules étrangères provoquant une abrasion ou des rayures sur les surfaces du roulement.
3. Désalignement : un désalignement excessif des arbres ou des boîtiers peut entraîner une charge inégale et une usure prématurée des rouleaux de roulement et des chemins de roulement.
4. Surcharge : l'application de charges dépassant la capacité nominale des roulements peut entraîner une déformation plastique ou une fracture des composants du roulement.
5.Corrosion : L'exposition à des environnements corrosifs peut entraîner des piqûres, de la rouille ou une dégradation chimique des surfaces de roulement, compromettant ainsi leurs performances.
6. Installation incorrecte : des procédures d'installation incorrectes, telles qu'une précharge insuffisante ou un mauvais alignement lors de l'assemblage, peuvent entraîner une défaillance prématurée.
Pour prévenir ou résoudre ces problèmes, les mesures suivantes peuvent être prises :
1. Maintenance appropriée : établir un système de gestion de maintenance centralisé qui intègre les calendriers de maintenance des roulements aux plans globaux de maintenance des équipements. Ce système doit inclure des rappels automatisés pour la lubrification, les inspections et les remplacements basés sur des intervalles prédéterminés ou des déclencheurs basés sur l'état. Utiliser des techniques de maintenance avancées, telles que la maintenance prédictive utilisant des algorithmes d'apprentissage automatique ou des technologies de surveillance à distance, pour prévoir les probabilités de défaillance des roulements et optimiser les activités de maintenance. pour une disponibilité maximale de l’équipement.
2. Installation correcte : développer des procédures d'installation standardisées comprenant des instructions détaillées étape par étape, des diagrammes annotés et des didacticiels vidéo pour répondre aux différents niveaux de compétence du personnel de maintenance. Effectuez des contrôles de validation après l'installation à l'aide d'outils de mesure de précision, tels que des indicateurs à cadran ou des dispositifs d'alignement laser, pour vérifier le bon alignement de l'arbre, la précharge des roulements et l'assise dans l'alésage du boîtier. Établir un processus interfonctionnel d'examen des installations impliquant les équipes d'ingénierie, de maintenance et d'assurance qualité pour garantir l'alignement avec les spécifications techniques et les meilleures pratiques de l'industrie.
3. Lubrification efficace : effectuez des audits de lubrification approfondis pour évaluer les pratiques de lubrification dans l'ensemble de l'organisation, en identifiant les domaines à améliorer tels que la sélection des lubrifiants, les méthodes d'application et les mesures de contrôle de la contamination. Mettez en œuvre un système de gestion centralisé de la lubrification utilisant des étiquettes RFID ou une technologie de codes-barres pour suivre l'utilisation des lubrifiants, les calendriers de réapprovisionnement et la compatibilité des équipements, rationalisant ainsi la gestion des stocks et réduisant le risque de mauvaise application. Collaborez avec les fournisseurs de lubrifiants et les fabricants d'équipements pour effectuer des tests de compatibilité des lubrifiants et optimiser les intervalles de lubrification en fonction des conditions de fonctionnement réelles et des commentaires sur les performances.
4. Protection de l'environnement : effectuer des évaluations des risques environnementaux pour identifier les sources potentielles de contamination, y compris les polluants atmosphériques, les points d'entrée d'eau et les voies d'exposition aux produits chimiques, et élaborer des stratégies d'atténuation ciblées adaptées à chaque catégorie de risque. Investissez dans des technologies d'étanchéité avancées, telles que des joints à labyrinthe ou des protecteurs de roulements magnétiques, capables de fournir une protection améliorée sans compromettre les performances des roulements ou les caractéristiques de dissipation thermique. Mettez en œuvre des protocoles de propreté stricts pour les activités de maintenance, y compris l'utilisation de salles blanches dédiées ou d'enceintes à air filtré pour le stockage, la manipulation et l'installation des roulements afin de minimiser l'introduction de contaminants dans les surfaces critiques des roulements.
5. Surveillance et inspection : Déployez une suite complète de capteurs et d'instruments de surveillance de l'état, notamment des accéléromètres, des sondes de température et des capteurs d'analyse d'huile, stratégiquement positionnés pour capturer des données en temps réel sur les paramètres d'état des roulements et les tendances de performances. Intégrez les données de surveillance de l'état aux systèmes de gestion des actifs de l'entreprise ou aux plateformes d'analyse basées sur le cloud pour faciliter l'agrégation, la visualisation et l'analyse des tendances centralisées, permettant ainsi une prise de décision proactive et une allocation des ressources basées sur des informations de maintenance prédictive. Mettez en œuvre des mécanismes de rétroaction en boucle fermée reliant les données de surveillance de l'état aux déclencheurs d'actions de maintenance, tels que la génération automatisée d'ordres de travail ou les commandes d'arrêt de l'équipement, pour garantir une intervention rapide en réponse aux problèmes émergents de dégradation des roulements.
Roulements à rouleaux coniques à une rangée appariés
Roulements à rouleaux coniques à une rangée appariés
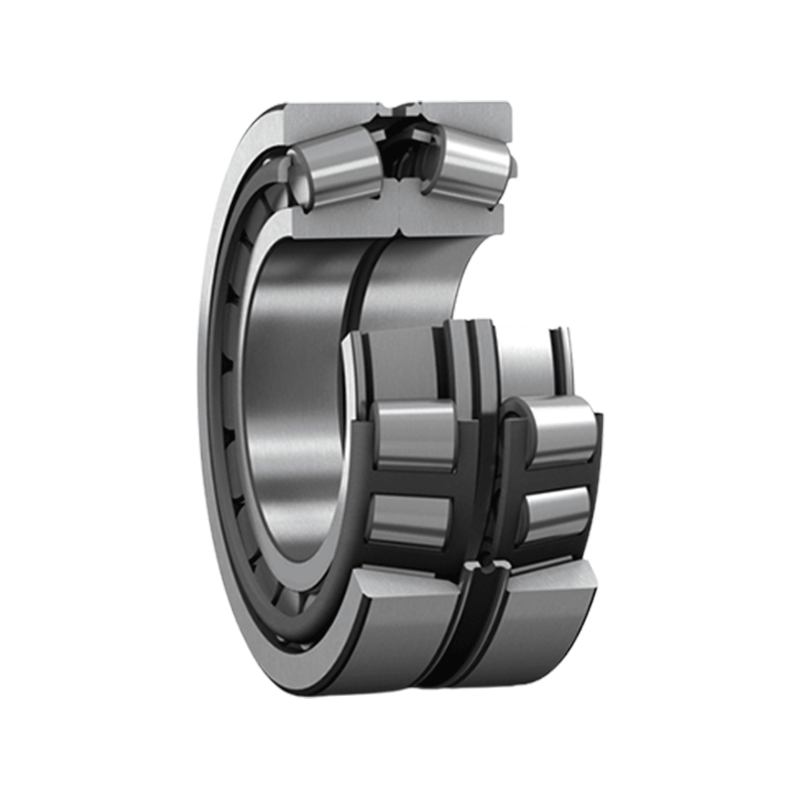